In regulated industries, we often encounter materials and processes that are highly sensitive to temperature and humidity. The storage of certain pharmaceuticals is one example. In these situations, temperature mapping, also referred to as thermal mapping, is a GxP method that is used to prevent the impact of temperature or humidity fluctuations to product quality. (Note that in this context, “thermal mapping” collectively refers to both temperature and humidity.)
As its name suggests, temperature mapping involves meticulous, three dimensional mapping of a controlled space, and can be done on the scale of individual process chambers like ovens or freezers, warehouses, or even across distribution and supply networks. In the context of GxP, temperature mapping is a way to validate and document that a temperature-controlled space is suitable for its purpose.
Temperature mapping should not be confused with the continuous temperature monitoring that would be a customary part of manufacturing, storage, and distribution of sensitive products. In temperature mapping, many data loggers are placed throughout the region of interest, more than would be used for typical monitoring, in order to develop a comprehensive picture of the conditions inside a space.
Mapping is done over a representative period of time, across a range of operating conditions (for example, with the space empty and loaded to capacity, as well as stress conditions like during door opening or power outages). The results of a mapping exercise can then be used to make a plan for routine monitoring, to recommend remedial action, or to develop an SOP for the arrangement of products in the space.
As with other GxP methods, temperature mapping is used in heavily regulated industries, including:
- Pharmaceutical and biotech manufacturing and testing
- Medical device manufacturing
- Laboratory operations
- Food and Beverages
- Warehousing, distribution, transportation, and other logistics involved with these industries
Why Temperature and Humidity Mapping Are Important
Accurate and thorough thermal mapping is important for a number of reasons, including:
- Safeguarding your products, consumers, and your finances. This is the primary goal, particularly in the case of drug or food storage. The results of a mapping study can be combined with knowledge of the effects of temperature and humidity on product effectiveness, safety, and overall quality to implement systems to prevent these products from experiencing harmful excursions.
- Maintaining regulatory compliance. In the U.S., the FDA regulates the safe handling and storage of foods, tissue and blood samples, pharmaceuticals, medical devices, and the components used to make them, through various parts of Title 21 of the CFR. This includes regulations for temperature and humidity control.
-
- For example, 21 CFR 211.142 states that drug products should be stored under “appropriate conditions of temperature, humidity, and light so that the identity, strength, quality, and purity of the drug products are not affected”. Regulations for food products and human tissues and cells can be found in 21 CFR 110.80 and 21 CFR 1271.60, respectively.
-
- FDA inspection citations from the last 10 years contain many instances of temperature and humidity control problems, mainly for foods, pharmaceuticals, and human tissue storage.
-
- Part of ensuring that these and other similar regulations are followed, and preventing regulatory action, is having a documented temperature mapping process, as well as evidence that the results of the mapping process are used to guide monitoring and control.
- Understanding the performance and capability of the HVAC systems. A thorough mapping study will determine whether the existing HVAC configuration can adequately control conditions in the space. Mapping includes stress testing the system at the extremes of conditions likely to be encountered, including loading, outside temperature and humidity variations, door opening, and power failures.
- Developing a data-based foundation for determining your monitoring needs in the future. This reduces cost and improves overall productivity, by allowing the implementation of efficient monitoring solutions that require minimal manual intervention. Having a complete understanding of the response of your temperature control systems under non-standard conditions also helps to reduce disruption when issues arise.
The importance of thermal mapping is demonstrated by the number of organizations that have published detailed guidelines, including the WHO, ISPE, USP, and PDA, among others.
Areas Where Mapping Is Critical
There are a number of specific areas where temperature mapping can be applied. Some of the most common include:
- Warehouses. Temperature mapping should be considered part of the OQ and PQ steps (operational qualification and performance qualification) when commissioning a new warehouse or storage area.
An example is the temperature mapping of a warehouse that is intended to store pharmaceuticals within a safe storage temperature window, based on prior stability studies, labeling, or recommendations from the manufacturer. The process would involve simultaneous measurements of temperature and humidity at many points within the 3 dimensional space of the warehouse, over a representative time period (usually a few days to a week). Measurement points are carefully selected to identify hot or cold spots, as well as to find trends, for example temperature variation horizontally or vertically across storage racks. Data would also be collected around potential problem areas, like heating/cooling vents, doorways, and skylights, and other critical points around data loggers used for feedback to the HVAC system.
Data from the mapping study data could then be used to identify areas where remedial action needs to be taken, or where products should not be stored. Any hot or cold spots identified in the mapping study could be used as locations for routine temperature monitoring going forward.
- Refrigerators, freezers, and cold rooms. For example, a refrigerator for the storage of time and temperature sensitive pharmaceutical products (TTSPPs). In this case, a mapping study would indicate areas of the refrigerator that would be unsafe for storage due to proximity to cooling coils or fans, or where to place temperature probes for feedback to temperature alarms.
- Transportation equipment. Dedicated shipping containers or other transport vehicles can be mapped in a similar way as a warehouse or cold room. For non-dedicated transport, like a mail truck, another option is to use insulated packaging that has itself been qualified using a mapping procedure that simulates the shipping process. For refrigerated products, temperature mapping of warehouses and shipping containers can be integrated to map the full “cold chain” of distribution.
- Processing areas. It is important that other areas where temperature-sensitive products could be stored are also mapped. Examples of these include manufacturing areas, packing and labeling areas, and loading docks.
- Stability chambers. Among other things, stability chambers (chambers with precisely controlled temperature, humidity, and other conditions) can be used for studies to determine the stability of drugs and drug packaging over time. Because the results of these studies will be used to make decisions about shelf stability and safe storage- and often later combined with temperature mapping of storage units- it is particularly important that these chambers be accurately mapped, understood, and monitored.
- Ultra-low temperature freezers. These freezers, which store samples at temperatures as low as -90 °C, are used to store human tissue, cells, and biologics. Due to the extreme sensitivity of the materials stored in them, the College of American Pathologists (CAP) requires temperature mapping of these freezers as part of their lab accreditation program. In this case, particular attention should be paid to the arrangement of samples inside the freezer, and the effect of opening the freezer door.
- Sterilizing equipment, for example, autoclaves used in aseptic processing, should be qualified using thermal mapping to ensure adequate temperature uniformity and sufficient lethal temperatures are reached during sterilization cycles. This will ensure that manufacturing parts and packaging materials (e.g. rubber stoppers, caps) are adequately sterilized prior to use in an aseptic environment.
- Ovens. Temperature mapping can be used for ovens at a range of scale, from small lab units to production scale, across various industries, including drug manufacturing and industrial scale food preparation. Ovens could be temperature mapped as part of a pre-shipment check, or mapped again after installation.
An example of a mapping exercise in an oven would be to measure the temperature at several points inside the oven, in the corners and the center, for example, at different setpoint temperatures. - Incubators. Incubators, and ovens to some extent, can involve a different aspect of mapping. In addition to storage at constant temperature, they involve heating a material up from ambient temperature. For storage, variation in air temperature typically represents the worst case scenario for variability, since it will change more quickly than the temperature of the product being stored. However, in incubators, where the temperature of the medium can be dynamic, it may be necessary to place temperature data loggers in the medium, in addition to measuring the temperature in the air space.
8 Steps to Getting Thermal Mapping Right
- Develop a test plan
-
- The plan should lay out the number and position of the temperature and humidity data loggers in three dimensions, based on a site survey.
- The main objective of placement is to characterize the variation across the entire storage space, and to be able to detect spatial trends.
- Considerations for data logger placement include:
- Dimensions of the space, and how much of the space is usable for product placement
- Storage arrangement like shelves, racking, and pallet stacking
- Location of active heating or cooling components
- Location of doors (internal and external) and skylights
- Possible temperature stratification over height in areas with high storage, such as mezzanines
- Any other sources of temperature nonuniformity.
- The plan should include mapping the space under empty and loaded conditions (OQ and PQ). Cyclical processes should also be considered, like shift changes or weekday versus weekend operations.
-
- However, the test plan should not only contain information on how to execute the measurements. A comprehensive plan also includes:
- Objectives of the mapping study. This section will drive decisions made in other parts of the study. For example, the decision of whether or not humidity measurements are performed in a warehouse could be based on a previous study of the effect of humidity on product stability.
- Description of the type of temperature and humidity measurement equipment that will be used. This equipment is selected based on factors like accuracy, response time, material compatibility, memory capacity, and measurement range. Temperature measurement could be done by self-contained loggers that measure, record, and store temperatures, or by remote data loggers that send data back to a central recording device. Note that for FDA-regulated operations, software should be compliant with 21 CFR Part 11.
- Rationale for selecting data logger placement, type, monitoring time, and other parameters of the study
- Summary of the site survey
- Acceptance criteria for temperature and humidity ranges, if applicable. For warehouse storage, this could be based on the known effects of temperature and/or humidity on stability. For ovens and sterilization equipment, it could be based on specifications of the process in which the equipment is used.
- Listing of IDs and serial numbers of individual data loggers and their location
- Template for the final report (this is particularly helpful if the same test plan will be used for multiple spaces)
- List of members of the mapping team, and a record of approvals and modifications to the plan
- However, the test plan should not only contain information on how to execute the measurements. A comprehensive plan also includes:
- Calibrate and program sensors and data loggers
- Calibration of the sensors and other data logging hardware and software is important, since the accuracy of the mapping data will be limited by any uncertainty in the measurements. In their thermal mapping guidance, the WHO states that temperature monitoring equipment should have a “NIST- traceable 3-point calibration certificate with a guaranteed error of no more than ± 0.5 °C at each calibration point”, or be calibrated by another method.
- The measurement range of the mapping study should be within the calibration points.
- Programming the measurement equipment involves setting a time interval for data collection, which varies widely based on the application. For warehouse mapping, this is typically in the range of 1-15 min, but shorter intervals may be needed for applications like freezers and sterilization equipment that are more sensitive to short temperature excursions.
- If the measurement data is stored locally on a logger, the total measurement time should not exceed its memory capacity.
- Place measurement equipment and execute measurements in test plan
- Data loggers should be placed according to the test plan, and any deviation from the plan should be documented. Each should be physically labeled with its ID.
- The duration of a mapping study depends on the nature of the space being mapped and the purpose of the mapping, but typically runs from 2 to 7 days, or longer in some cases. Small units that are less sensitive to normal cycles in ambient temperatures, like ovens or freezers, may require less time.
- It is important that recording start simultaneously for all locations, so that all temperature records are synchronized.
- Retrieve measurement equipment
- While collecting the data loggers, placement and ID should be double-checked, and any deviation from the test plan should be documented.
- Any unusual observations, like measurement equipment moving out of place or other changes since the start of the test, should be documented.
- Download and analyze data
- Initial data analysis should include:
- Overall range in temperature and humidity over the mapping period, including over individual data loggers, as well as any general trends (temperature and humidity variation over height, or variation as a function of distance from doorways or temperature control components, for example)
- The ability of the active temperature control systems to maintain conditions relative to the acceptance criteria
- Location and temperature of hot and cold spots. “Hot spot” and “cold spot” can have a specific meaning in the context of temperature mapping, namely the locations of measured temperature extremes that are still within the acceptance criteria.
- Temperature and humidity averages for individual data loggers, which can be useful to quickly compare between locations. This could be simply the mean temperature over time, or some more complex temperature averaging scheme such as the mean kinetic temperature (MKT).
- Keep in mind when analyzing data that the uncertainty given by probe calibration is only one source of uncertainty in the measurement, and that the accuracy and precision of the measurement data may be limited by other factors.
- Post-calibrate measurement equipment
- Because the analysis and conclusions of the study are only as good as the sensor accuracy, data logging systems should be recalibrated after the mapping study to confirm they were accurate throughout the study period.
- Complete mapping report
- The report should contain the following:
- Objectives of the mapping project (a restatement from the test plan)
- Summary of the results, based on the data analysis done in Step 5
- Summary of Deviation Reports if necessary
- Analysis and confirmation on whether acceptance criteria were met
- Conclusions and recommendations
- Appendices for raw data, calibration records, site surveys, and any other documents prepared for the mapping exercise
- Make Recommendations
- Based on the results in the mapping report and the objectives of the study, recommendations could include:
- Remedial action, in terms of changes to the heating/cooling apparatus like fans, air outlets, or heating coils, adding humidifiers or dehumidifiers, or changes to the SOP for the building or equipment
- Placement of data loggers for routine monitoring. For example, it may be desirable to place data loggers in hot and cold spots so that the full range of temperatures is represented during monitoring. Mapping can also indicate the best placement of an exemplar, or temperature probe that is representative of the average across the entire space.
- Determining setpoints for alarms or feedback to active temperature control. Note that the results of a thermal mapping study might indicate that the appropriate temperature setpoints, as measured at one fixed point, are not identical to the overall temperature limits for the space. For example, using control setpoints of 18-22 °C as measured by a sensor in the middle of the space might ensure that no part of a space goes outside of 15-25 °C. For measurements done for control purposes, it may also be recommended to place sensors in a temperature buffer such as a vial of ethylene glycol.
- Safe or unsafe locations for materials based on their sensitivity
- Changes to stacking or other arrangement of products to ensure minimal impact on temperature control (to maintain good airflow, for example)
- Response plan for power outages or other equipment failures (if these were tested as part of the mapping process)
These steps, with appropriate modifications, can be used across many different temperature controlled spaces.
It is recommended to repeat mapping periodically, or after significant changes to the space or the temperature control system. For spaces that are sensitive to seasonal variation in temperature and humidity, it may also be necessary to repeat mapping at different times of the year to represent the extremes of outdoor temperature variation. Note that while climate data is useful in determining where mapping is needed, it is not a substitute for mapping.
Should you bring in outside expertise for a thermal mapping project?
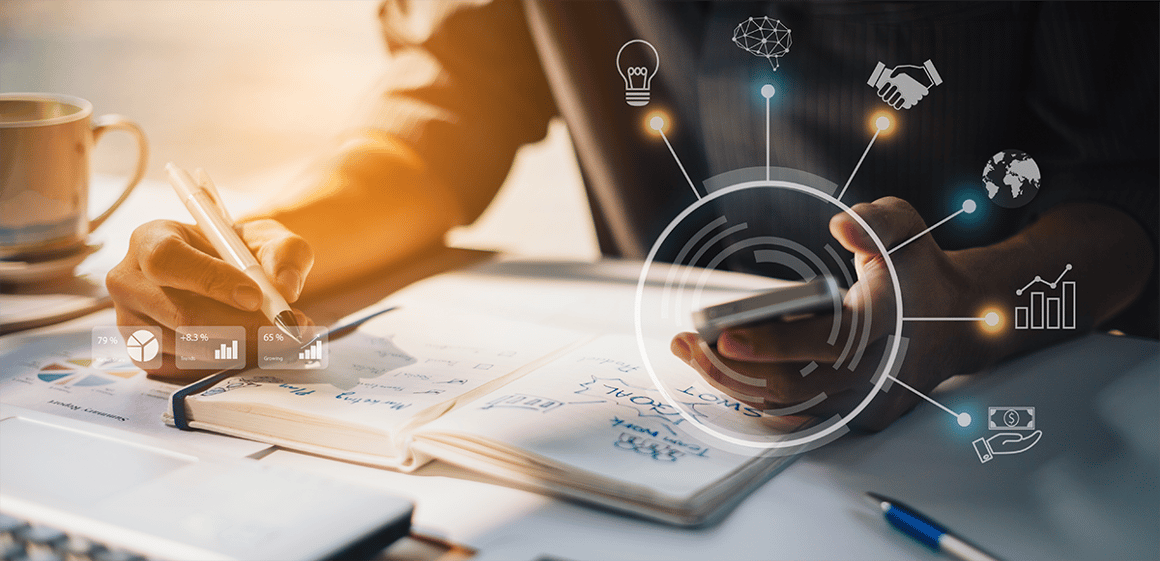
There are three main reasons for calling on outside experts for help with thermal mapping projects. The first is cost. Thermal mapping generally requires specialized equipment and software, and the use of many more temperature monitors than would normally be used during routine operations. For most companies, this equipment would have a very low utilization rate if mapping was performed in-house. In addition, outside experts can handle calibration and maintenance of the measuring equipment, avoiding the need for third-party calibration.
The second reason is that most companies do not have the required expertise on staff to plan, execute, and interpret the results of a thermal mapping project. As with many aspects of GxP, these projects are highly detail-oriented and require rigorous documentation.
The complexities of the mapping process leads to a third reason organizations often seek outside help: time. Because of the detailed nature of the work, a typical mapping project can require 130-250 person-hours. The best way to ensure the creation of sound test plans that generate high quality reports and data-based recommendations is to rely on experts who routinely perform this work. This also minimizes the likelihood of mistakes during mapping, which can result in costly fixes or regulatory actions later on.
Conclusion
Thermal mapping is a detail-oriented, rigorous process that should be part of the qualification of any new temperature-controlled chamber or storage space. Correctly working through the mapping process will lead to a more efficient temperature control and monitoring scheme, less downtime and product loss due to excursions, and ultimately contribute to an overall GxP environment that ensures product quality and regulatory compliance.
Questions about thermal mapping or other environmental monitoring needs? Contact Dickson today.
About the author: Before coming to Dickson, Director of Services Antoine Nguyen spent more than 18 years in quality and validation roles in the pharmaceutical and medical device industries.